Technical Assistance & Troubleshooting
Visor enhances quality control by helping teams follow proper procedures, automating documentation, and providing an extra set of eyes.
Integrated with your QMS, it gives inspectors real-time access to checklists, AR overlays for defect detection, and seamless tools for logging and collaboration.
Integrated with your QMS, it gives inspectors real-time access to checklists, AR overlays for defect detection, and seamless tools for logging and collaboration.
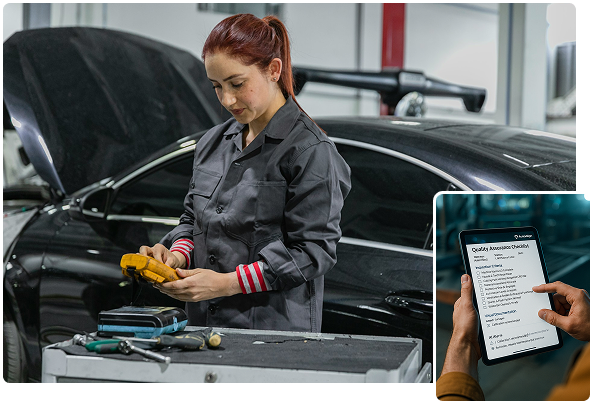
Increased Automation, Fewer Errors
Many service technicians must still consult paper manuals and rely on manual documentation for checklists. This can increase workflow inefficiencies and error rates.
AutoAlign Visor enables in-context documentation retrieval. Visor provides a hands-free, intuitive interface to connect your company's digital content (e.g. videos, diagrams, specifications) with field technicians.
AutoAlign Visor enables in-context documentation retrieval. Visor provides a hands-free, intuitive interface to connect your company's digital content (e.g. videos, diagrams, specifications) with field technicians.
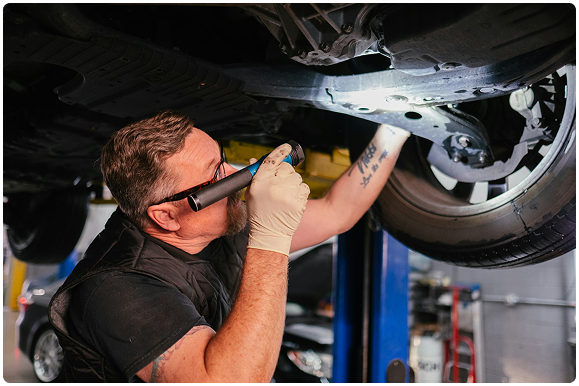
Reduced Downtime Due to Maintenance and Repairs
The downtime required to maintain and repair equipment can be enormously costly.
AutoAlign Visor enables engineers to efficiently address issues by leveraging AI for troubleshooting. It provides real-time machine data, 3D models, detailed instructions from backend systems, and video tutorials superimposed onto machines requiring attention. Workers benefit from AI-supported real-time assistance, and remote technicians can observe their view to offer live support.
AutoAlign Visor enables engineers to efficiently address issues by leveraging AI for troubleshooting. It provides real-time machine data, 3D models, detailed instructions from backend systems, and video tutorials superimposed onto machines requiring attention. Workers benefit from AI-supported real-time assistance, and remote technicians can observe their view to offer live support.
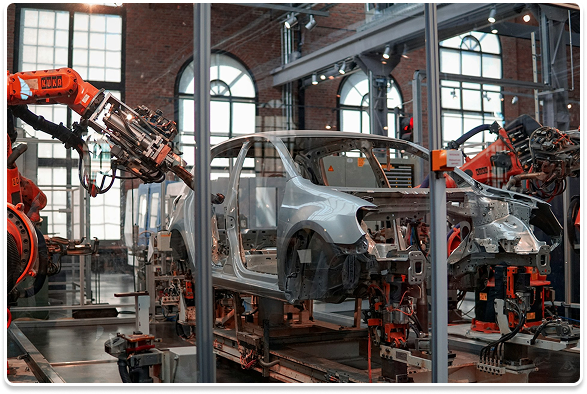
Quality Assurance and Control (QA)
Visor enhances quality control by ensuring key steps are followed, automating records to free up focus for execution, and serving as an extra set of eyes.
Traditional QA methods often rely on manual documentation, increasing the risk of errors and missed defects. With AutoAlign Visor integrated into your QMS, inspectors can access digital checklists, automate compliance logs, use AR overlays to spot defects, contact technicians, and instantly research or upload findings.
Traditional QA methods often rely on manual documentation, increasing the risk of errors and missed defects. With AutoAlign Visor integrated into your QMS, inspectors can access digital checklists, automate compliance logs, use AR overlays to spot defects, contact technicians, and instantly research or upload findings.
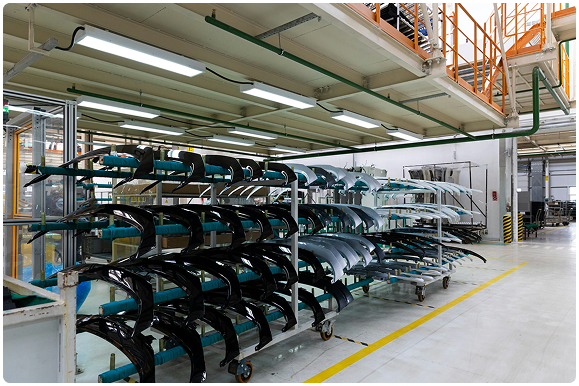
Real-Time Training and Guidance
The lack of training, experience, and access to information increases costs whether in the form of quality assurance, ineffective repairs, lost reputation or follow-up visits.
AutoAlign Vizor allows effective training on-site. Technicians get interactive, AI-powered feedback, can bring up resources quickly, or learn interactively from remote instructors or senior staff.
AutoAlign Vizor allows effective training on-site. Technicians get interactive, AI-powered feedback, can bring up resources quickly, or learn interactively from remote instructors or senior staff.
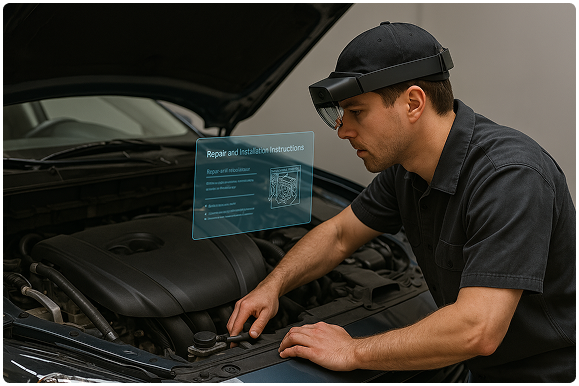
Compliance and SOPs
Provide in-context guidance for complicated SOPs and monitor adherence to procedures, recording compliance
Alert proactively when there are deviations or safety issues detected.
Alert proactively when there are deviations or safety issues detected.
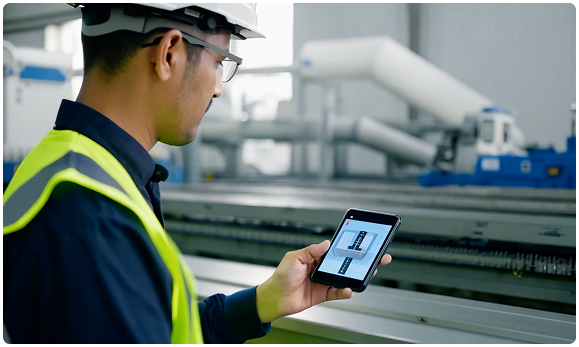
Safety
Directly alert employees proactively when there are deviations or safety issues detected.
Ensure safety is clearly articulated in-context during training and while conducting procedures.
Ensure safety is clearly articulated in-context during training and while conducting procedures.
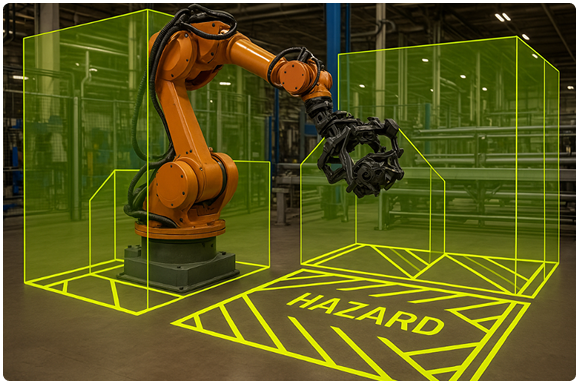